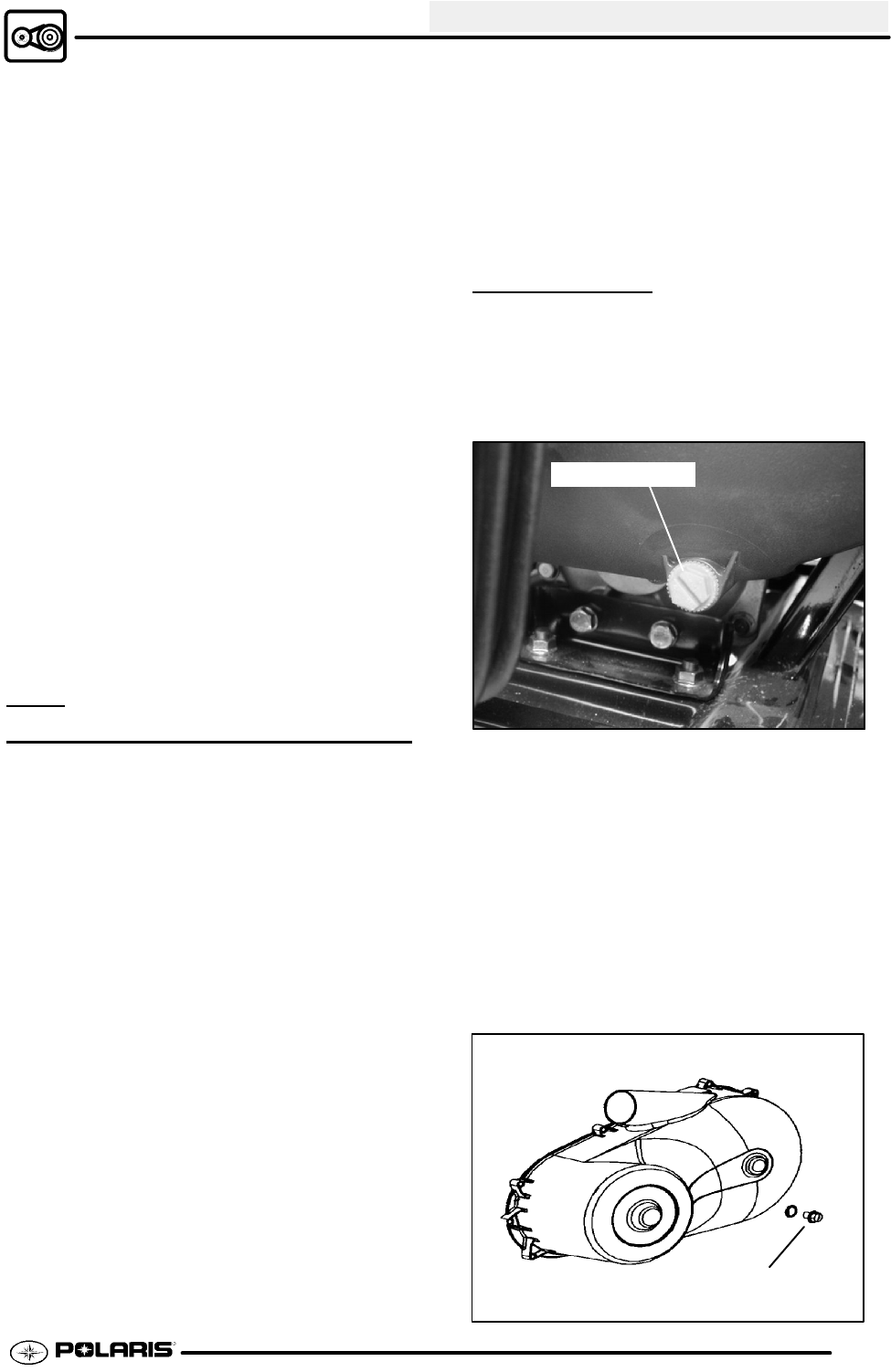
CLUTCHING
6.3
DRIVEN CLUTCH OPERATION CONT’D
As engine RPM and horsepower increase, the load
from the drive belt increases, resulting in the belt
rotating up toward the outer diameter of the drive
clutch sheaves and downward into the sheaves of the
driven clutch. This action, which increases the driven
clutch speed, is called upshifting.
Should the throttle setting remain the same and the
vehicle is subjected to a heavier load, the drive belt
rotates back up toward the outer diameter of the
driven clutch and downward into the sheaves of the
drive clutch. This action, which decreases the driven
clutch speed, is called backshifting.
In situations where loads vary (such as uphill and
downhill) and throttle settings are constant, the drive
and driven clutches are continually shifting to maintain
optimum engine RPM. At full throttle a perfectly
matched PVT system should hold engine RPM at the
peak of the power curve. This RPM should be
maintained during clutch upshift and backshift. In this
respect, the PVT system is similar to a power
governor. Rather than vary throttle position, as a
conventional governor does, the PVT system
changes engine load requirements by either
upshifting or backshifting.
PVT
MAINTENANCE/INSPECTION
Under normal operation the PVT system will provide
years of trouble free operation. Periodic inspection
and maintenance is required to keep the system
operating at peak performance. The following list of
items should be inspected and maintained to ensure
maximum performance and service life of PVT
components. Refer to the troubleshooting checklist at
the end of this chapter for more information.
1. Drive to Driven Clutch Offset, Belt Width. See
Page-6.16--6.18
2. Drive and Driven Clutch Buttons and
Bushings, Drive Clutch Shift Weights and
Pins, Drive Clutch Spider Rollers and Roller
Pins, Drive and Driven Clutch Springs. See
Pages 6.11-6.12
3. Sheave Faces. Clean and inspect for wear.
4. PVT System Sealing. Refer to appropriate
illustrations and photos. The PVT system is air
cooled by fins on the drive clutch stationary
sheave. The fins create a low pressure area inthe
crankcase casting, drawing air into the system
through an intake duct. The opening for this
intake duct is located at a high point on the vehicle
(location varies by model). The intake duct draws
fresh air through a vented cover. All connecting
air ducts, as well as the inner and outer covers,
must be properly sealed to ensure clean air is
being used for cooling the PVT system. This also
will prevent water and other contaminants from
entering the PVT area. A sealed PVT is
especially critical on units subjected to frequent
water forging.
PVT DRYING
NOTE: If operating the ATV through water, be sure
to check the PVT cover and other ATV components
for water ingestion. The ATV should be checked
immediately. Refer to Owner’s Manual for Safe
Riding Tips.
PVT Drain Plug
To drain any water that may be trappedinside the PVT
cover, simply remove the PVT drain plug and O--ring
located on the bottom of the PVT cover and let the
water drain out. The PVT drain plug is shown below.
To further expel water in the PVT cover and to dry out
the PVT system, shift the transmission to neutral and
rev engine slightly to expel the moisture. This will also
air-dry the belt and clutches. Allow engine RPM to
settle to idle speed, shift transmission to lowest
available range and test for belt slippage. Repeat as
needed. Operate ATV in lowest available range for a
short period of time until PVT system is dry.
PVT Drain Plug & O--ring