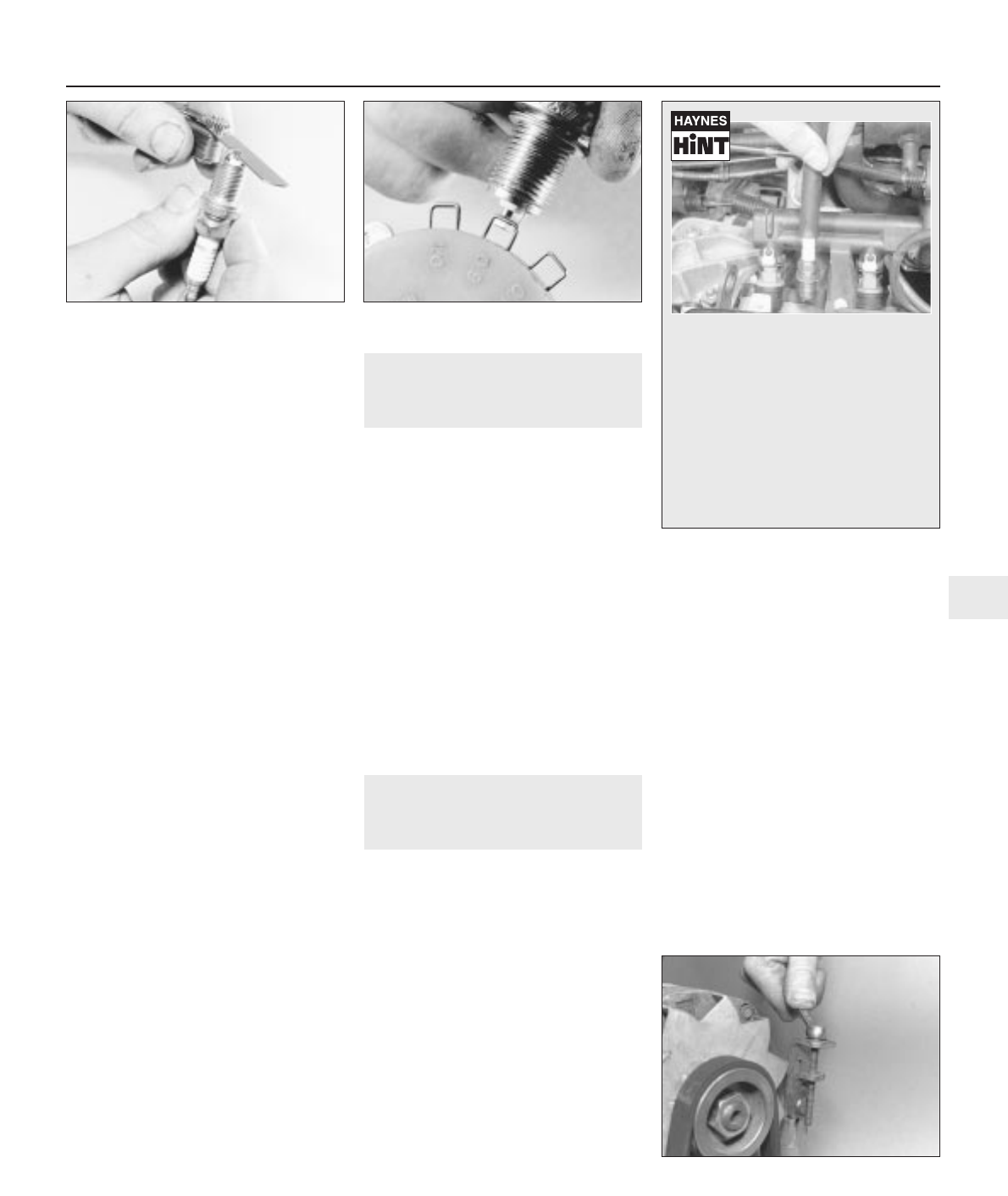
Keep the socket aligned with the spark plug -
if it is forcibly moved to one side, the ceramic
insulator may be broken off. As each plug is
removed, examine it as follows.
5 Examination of the spark plugs will give a
good indication of the condition of the engine.
If the insulator nose of the spark plug is clean
and white, with no deposits, this is indicative
of a weak mixture or too hot a plug (a hot plug
transfers heat away from the electrode slowly,
a cold plug transfers heat away quickly).
6 If the tip and insulator nose are covered
with hard black-looking deposits, then this is
indicative that the mixture is too rich. Should
the plug be black and oily, then it is likely that
the engine is fairly worn, as well as the mixture
being too rich.
7 If the insulator nose is covered with light tan
to greyish-brown deposits, then the mixture is
correct and it is likely that the engine is in
good condition.
8 The spark plug electrode gap is of
considerable importance as, if it is too large or
too small, the size of the spark and its
efficiency will be seriously impaired. The gap
should be set to the value given in the
Specifications at the beginning of this Chapter.
9 To set the gap, measure it with a feeler
blade, and then bend open, or closed, the
outer plug electrode until the correct gap is
achieved (see illustration). The centre
electrode should never be bent, as this may
crack the insulator and cause plug failure, if
nothing worse. If using feeler blades, the gap
is correct when the appropriate-size blade is a
firm sliding fit.
10 Special spark plug electrode gap
adjusting tools are available from most motor
accessory shops, or from some spark plug
manufacturers (see illustration).
11 Before fitting the spark plugs, check that
the threaded connector sleeves are tight, and
that the plug exterior surfaces and threads are
clean (see Haynes Hint).
12 Remove the rubber hose (if used), and
tighten the plug to the specified torque using
the spark plug socket and a torque wrench.
Refit the remaining spark plugs in the same
manner.
13 Connect the HT leads in their correct
order, and refit any components removed for
access.
8 Throttle and choke cable
lubrication and adjustment
1
1 The throttle cable is connected to a
spring-loaded reel which pivots on the face of
the cylinder head. On certain models, the reel
then operates the throttle lever on the
carburettor through a plastic balljointed
control rod.
2 Sparingly apply a few drops of light oil to
the throttle spindles, linkage pivot points and
to the cable itself. Similarly lubricate the
exposed ends of the choke cable (where
fitted).
3 Check that there is a small amount of
slackness in the cable so that the throttle
linkage closes fully with the accelerator pedal
released. Also check that full throttle can be
obtained with the accelerator pedal fully
depressed.
4 If there is any doubt about the cable
adjustment, refer to the relevant Parts of
Chapter 4 for the full adjustment procedure.
9 Auxiliary drivebelt check and
renewal
2
1 Depending on specification, either one or
two auxiliary drivebelts are fitted. Where two
belts are fitted, it will obviously be necessary
to remove the outer belt in order to renew the
inner belt.
Checking the auxiliary drivebelt
condition
2 Apply the handbrake, then jack up the front
of the car and support it on axle stands.
Remove the right-hand front roadwheel.
3 From underneath the front of the car, prise
out the retaining clips, and remove the plastic
cover from the wing valance where necessary,
to gain access to the crankshaft
sprocket/pulley bolt.
4 Using a suitable socket and extension bar
fitted to the crankshaft sprocket/pulley bolt,
rotate the crankshaft so that the entire length
of the drivebelt(s) can be examined. Examine
the drivebelt(s) for cracks, splitting, fraying or
damage. Check also for signs of glazing (shiny
patches) and for separation of the belt plies.
Renew the belt if worn or damaged.
5 If the condition of the belt is satisfactory,
check the drivebelt tension as described below.
Auxiliary drivebelt - removal,
refitting and tensioning
Removal
6 If not already done, proceed as described
in paragraphs 2 and 3.
7 Disconnect the battery negative lead.
8 Slacken both the alternator upper and lower
mounting nuts/bolts (as applicable).
9 Push the alternator toward the engine until
the belt is slack then slip the drivebelt from
the pulleys. Where an adjuster bolt is fitted,
back off the adjuster to relieve the tension in
the drivebelt, then slip off the belt (see
illustration).
Refitting
10 If the belt is being renewed, ensure that
the correct type is used. Fit the belt around
the pulleys, and take up the slack in the belt
Every 12 000 miles or 12 months 1•11
1
7.9 Measuring the spark plug gap with a
feeler blade
7.10 Measuring the spark plug gap with a
wire gauge
9.9 Slackening the alternator adjuster bolt
to release the auxiliary drivebelt
It is very often difficult to insert spark
plugs into their holes without cross-
threading them. To avoid this
possibility, fit a short length of 5/16 inch
internal diameter rubber hose over the
end of the spark plug. The flexible hose
acts as a universal joint to help align
the plug with the plug hole. Should the
plug begin to cross-thread, the hose
will slip on the spark plug, preventing
thread damage to the aluminium
cylinder head