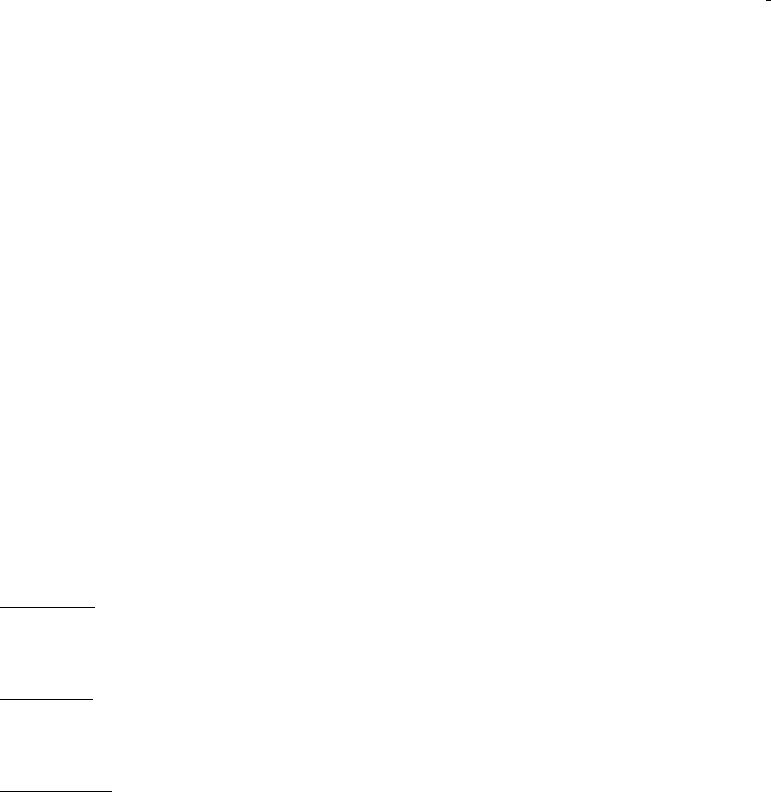
CHAPTER 1 – THEORY OF OPERATION
1-1 Introduction
To understand why certain steps have to be performed while running this motion
simulator you should know how the unit does what it does. You also need to know how
each part plays its part so when something should go wrong, it can be corrected with
minimum down time.
NOTE: The Inverters must be matched at the factory to the power available in the field
installation. The motors can be rewired for various inputs but the inverters
cannot.
1-2 ELECTRICAL
1-2A Input Power: 115/20 VAC one phase 60hz for computer, blowers, projector, audio amplifiers.
208/440/477 VAC three phase, for drive motors.
.
1-2B Power Box: Contains the following;
1. Three frequency drive invertors that are the same
a. Pitch
b. Roll
c. Lift
2. Frequency drive for the counterweight motor
3. Three brake control relays
4. CPU interface distribution box, serial control bus
5. Main power relay contactor and thermal overload protect
6. Receptacles for all connections
7. Cooling fan
8. Brake resistors for the big drive motors (three)
1-2C Electro Magnetic Interference (EMI)
EMI is a problem when you have high current wires laying parallel with low current/voltage wires. When
the magnetic field about a wire changes, that change induces voltage spikes or signal interference into
associated wires. If this becomes a problem there are ways to correct this. One, is limiting induction on
other wires by using shielded cables and connections. The other method is to space wires apart or run them
ninety degrees to each other. In this system we use both methods to limit power interference into video,
audio and control signal cabling.
1-2D Roll Axis
Roll Motor: Three phase AC motor. Mounted in the center weldment with four bolts and shims for
spacing. Roll shaft and hub assembly gets mounted through the center of the gearbox. Gearbox pre-filled
at factory. A key transmits torque to roll shaft.
Roll Brake:
Mounted on the end of drive motor. Stops motor rotation and holds the axis where last left. It
receives 220 VAC to the rectifier inside the enclosure. The coil is a 220 VDC unit. It has a manual release
lever.
Roll Encoder:
Mounted on the end of the roll motor shaft. Sends roll position of the platform back to the
computer via the interface board and motion control board.