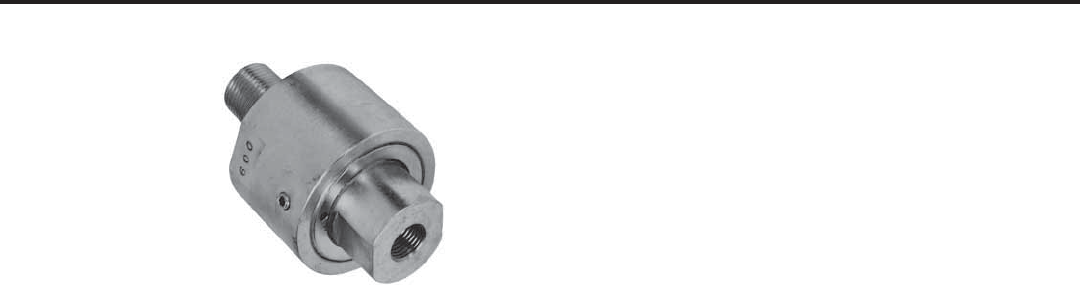
19
CONTROL OPTIONS
Two basic types of control are available:
120 V ac contact closure (options 3, 4, 5, and 6)
and milliamp or dc analog modulating (options 7
and 8). Each option is described below.
Open / close option 3: For simple 2-position
control using manual push-buttons or an
automatic controller. Preset travel limit switches
provide open / close operation upon closure of an
automatic controller or manually operated switch.
Travel limits are adjustable over the full range of
travel and have a repeatability of 0.1°.
Multi-position option 4: Adjustable, cam
operated switches provide up to five discrete stop
positions upon closure of an automatic controller
or manually operated switch. Three, four, and
five predetermined position settings are possible,
with positioning repeatability of 1° over the range
of operation.
Direct ac control option 5: Operated in forward
/ reverse from a remote location; includes a 1,000
ohm film potentiometer for remote feedback.
Direct ac control option 6: Provides
continuous positioning capability over the full
range of drive travel by direct ac from either
an automatic controller or manually operated
switches. Includes Contactless Position Sensor
(CPS-2) for feedback and position indication.
Modulating option 7: For automatic operation
in response to milliamp or V dc analog control;
includes a film potentiometer for position sensing
and feedback to the Electronic Signal Receiver
(ESR-4).
Modulating option 8: For automatic operation,
as in option 7, above; includes Contactless
Position Sensor (CPS-2) for position sensing and
feedback to the ESR-4.
INPUT: ELECTRONIC SIGNAL
RECEIVER (ESR-4)
Beck modulating drives are equipped with
precision electronic control modules (ESR-4)
to receive conventional 4–20 mA or 1–5 V dc
control
signals directly, eliminating the need for contact
protection devices, relays, switches, and revers-
ing starters.
The ESR-4 provides for drive control with
analog control systems, and is designed to
operate continuously in temperatures up to
185°F.
A feedback signal from either the CPS-2 or
a film potentiometer is compared to the input
HANDWHEEL
Every Beck Group 14 linear drive is furnished
with a Handwheel for operation of the valve
without electrical power. Its solid construction
design includes no spokes or projections, and
turns at a safe, slow speed. The Handwheel
is located at the bottom of the control motor
housing. The Handwheel is coupled directly
to the motor shaft and rotates when the motor
runs. Manual operation of the Handwheel (with
electric Handswitch in STOP position) turns
the motor and the rest of the drive train without
incorporating a clutch.
HANDSWITCH
A local electric Handswitch is provided on
Beck drives to permit operation at the valve,
independent of the controller. As a safety feature,
the Handswitch is designed so that the controller
can operate the drive only when it is in the AUTO
position. The sequence of the Handswitch is:
AUTO, STOP, RETRACT, STOP, EXTEND.
In the AUTO position, two contacts are closed
and the ESR-4 or external controller contact
completes the control circuit.
In the RETRACT or EXTEND positions,
contacts are closed to operate the drive
independently of the controller.
In the STOP position, all contacts remain open.
SWITCHES
Two end-of-travel switches and up to four
optional auxiliary switches are provided on Group
14 drives. Switch cams are clamped onto the
control shaft, which rotates in relation to the output
shaft. Cam position is field-adjustable. Switches
are enclosed in high-impact thermoplastic.
Switches are rated 6 A, 120 V ac (0.5 A, 125 V
dc). All auxiliary switch connections are made on
the terminal board.
Figure 4
Tight-Seater™
Continued