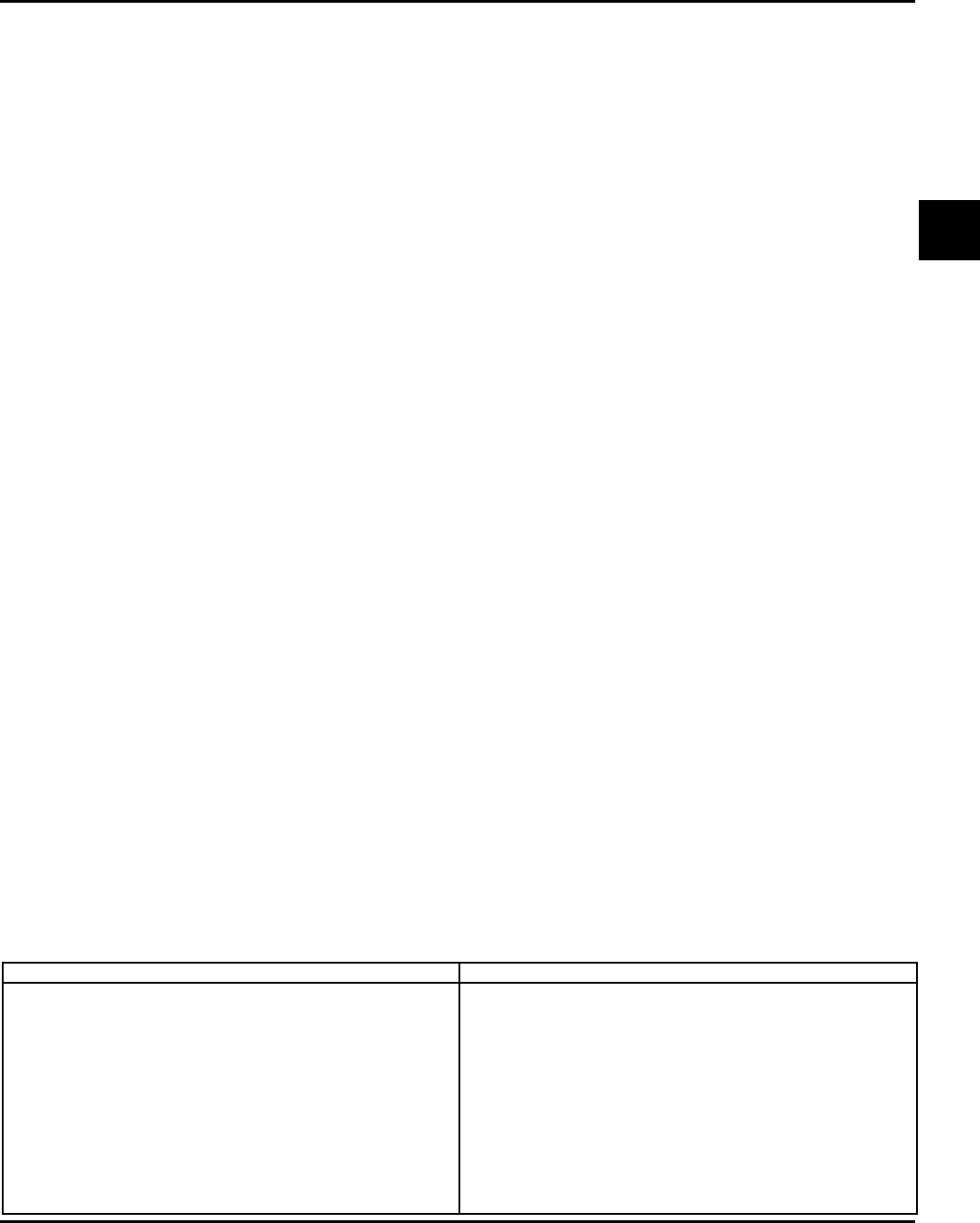
3.3
Section 3
Troubleshooting
3
NOTE: It is good practice to drain oil at a location
away from the workbench. Be sure to
allow ample time for complete drainage.
Cleaning the Engine
After inspecting the external condition of the engine,
clean the engine thoroughly before disassembling it.
Also clean individual components as the engine is
disassembled. Only clean parts can be accurately
inspected and gauged for wear or damage. There are
many commercially available cleaners that will quickly
remove grease, oil, and grime from engine parts. When
such a cleaner is used, follow the manufacturer’s
instructions and safety precautions carefully.
Make sure all traces of the cleaner are removed before
the engine is reassembled and placed into operation.
Even small amounts of these cleaners can quickly
break down the lubricating properties of engine oil.
Basic Engine Tests
Crankcase Vacuum Test
A partial vacuum should be present in the crankcase
when the engine is operating. Pressure in the
crankcase (normally caused by a clogged or improperly
assembled breather) can cause oil to be forced out at
oil seals, gaskets, or other available spots.
Crankcase vacuum is best measured with either
a water manometer (Kohler Part No. 25 761 02-S)
or a vacuum gauge (Kohler Part No. 25 761 22-S).
Complete instructions are provided in kits.
Test the crankcase vacuum with the manometer as
follows:
1. Insert the stopper/hose into the oil fill hole. Leave
the other tube of manometer open to atmosphere.
Make sure the shut-off clamp is closed.
2. Start the engine and run at no-load high idle
speed (3200 to 3750 RPM).
3. Open the clamp and note the water level in the
tube.
The level in the engine side should be a minimum
of 10.2 cm (4 in.) above the level in the open
side.
If the level in the engine side is less than
specified (low/no vacuum), or the level in the
engine side is lower than the level in the open
side (pressure), check for the conditions in the
table below.
4. Close the shut-off clamp before stopping the
engine.
Compression Test
A compression test is best performed on a warm
engine. Clean any dirt or debris away from the base
of the spark plugs before removing them. Be sure the
choke is off, and the throttle is wide open during the
test. Compression should be at least 160 psi and
should not vary more than 15% between cylinders.
Cylinder Leakdown Test
A cylinder leakdown test can be a valuable alternative
to a compression test. By pressurizing the combustion
chamber from an external air source you can
determine if the valves or rings are leaking, and how
badly.
Kohler Part No. 25 761 05-S is a relatively simple,
inexpensive leakdown tester for small engines. The
tester includes a quick disconnect for attaching the
adapter hose and a holding tool.
Possible Cause Solution
1. Replace breather assembly (valve cover).
2. Replace all worn or damaged seals and gaskets.
Make sure all fasteners are tightened securely.
Use appropriate torque values and sequences
when necessary.
3. Recondition piston, rings, cylinder bore, valves,
and valve guides.
4. Repair/replace restricted muffler/exhaust system.
1. Crankcase breather clogged or inoperative.
2. Seals and/or gaskets leaking. Loose or
improperly torqued fasteners.
3. Piston blowby or leaky valves. (Confirm by
inspecting components.)
4. Restricted exhaust.
No Crankcase Vacuum/Pressure in Crankcase