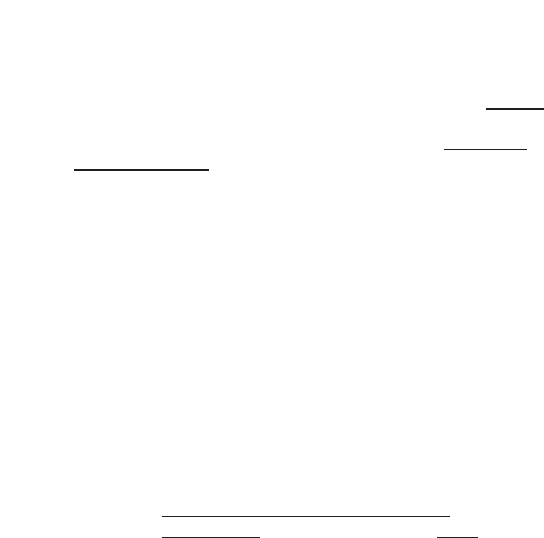
2
CAUTION - WELD END VALVES
Weld end valves for schedule 10 and heavier pipe require
actuator removal prior to welding in line. Schedule 5 and
lighter pipe and tubing may be welded with automatic
equipment only without removing the actuator. The valve
must be in the open position and properly purged with an
inert gas. Manual welding requires actuator removal for all
tubing gages and pipe schedules.
1 INSTALLATION
1.1 Dia-Flo
®
diaphragm valves may be installed in any
orientation. For horizontal piping systems to be
drained through the valve, install the valve stem
between 0 and 30 degrees above horizontal. Note:
Pure-Flo
®
valves have either raised hash marks
(castings) or small machined dots (forgings) on
the valve body to indicate the correct drain angle.
Locate these marks at the 12 o’clock position to
achieve the optimum drain angle.
1.2 Prior to pressurization (with the valve
slightly open), tighten the bonnet bolts in
a crisscross pattern in accordance with
Table 1.
Retightening 24 hours after the system reaches oper-
ating temperature and pressure is recommended. If
leakage occurs at the body/diaphragm seating area,
immediately depressurize system and tighten bonnet
bolts as noted above. If leakage continues,
diaphragm replacement is required. Follow applica-
ble steps in Section 3.6.1, 3.7.1 or 3.8.1.
1.3 The travel stop (closing stop), if equipped, is factory
set and should not require adjustment at time of
installation. However, if adjustment is required, see
section 4.1.
1.4 Maximum valve operating pressure is 150 PSIG
(10.34 bar). This pressure is applicable up to 100
degrees F (38 degrees C), valves at maximum pres-
sure cannot be used at maximum temperatures.
CAUTION: The actuator size/configuration may limit
the actual operating pressure, consult Engineering
Catalog for actuator sizing. Consult factory or
Engineering Catalog for vacuum operation.
1.5 Air line connections should be made with care as
damage may occur to the standard plastic actuator
covers. Connection size is 1/8” NPT for 1/4” through
2” (DIN 8 - 50) and 1/4” NPT for 3” and 4” (DIN 80 -
100).
1.6 3” and 4” (Series 33 and 47) (DIN 80 and 100)
Advantage
®
actuators must not be lifted by the
air fittings. Prepare an eye bolt with a 0.625“ -18
female thread to attach to the adjusting bushing,
use a hoist to lift with this attachment. (Series 47
only)
1.7 The stainless steel bonnet Advantage
®
Actuator
(1/4”-2”) (DIN 8-50) can have the air inlets posi-
tioned in any quadrant. The actuator must be
removed from the valve body and the actuator
diaphragm replacement steps followed. Unthread
the bushing, lift and rotate the lower cover to posi-
tion the air inlet in the desired quadrant. Press down
on the cover to insure it sits square on the bonnet
and re-assemble the bushing to the proper torque.
Bio-tek: . . . . . . . . . . . . . . . . . . . . . . . . . . .150 in-lb
.50 - 1.0”: . . . . . . . . . . . . . . . . . . . . . . . . .200 in-lb
1.5/2.0”: . . . . . . . . . . . . . . . . . . . . . . . . . .240 in-lb
2 OPERATION & ADJUSTMENT
2.1 The Advantage
®
actuator is a spring-and diaphragm,
or double acting diaphragm, pneumatic actuator.
The actuator model number is located on the ITT
i.d. tag. The model number is a four or five digit
number defining the actuator as follows:
AXYYZ
A = Advantage” Actuator
X = 1 Direct Acting (Spring to Open)
X = 2 Reverse Acting (Spring to Close)
X = 3 Double Acting
YY = Nominal Size. Available sizes
(approximate effective diaphragm area in
square inches): #03, 05, 08, 16, 33, 34, 47, 48.
Z = 6 60 PSI Spring Package
Z = 9 90 PSI Spring Package
Z is only used for Reverse Acting Units
(Spring to Close) sizes 1/4” - 2” (DIN 8 - 50). Note
that for the 3” & 4” actuators A233, A247 repre-
sent a 60 PSI Spring Package and A248 represents a
80 PSI Spring Package. A234 represents a 90 PSI
Package.
2.2 Maximum permitted air supply pressure is
90 psig (6.2 bar, 620 kPa).
ACTUATOR PRESSURE RATING
The Advantage actuator has a pressure rating of 90 psig.
However, the actuator will withstand pressures well in excess of
the rated pressure without risk of bursting.
Maintaining operating pressure at or below 90 psig will ensure
optimum life of the operating components, such as the actuator
diaphragm. However, operation at pressures up to 95 psig, for
limited periods of time, will not noticeably affect the life of
these components.
2.3 For operation and adjustment of actuator acces-
sories, see Section 4.0.
2.4 Valve and actuator travel are shown in Table 2.
3 MAINTENANCE
3.1 Periodic Inspection
Periodically inspect condition of external valve parts.
Replace all parts showing excessive wear or corro-
sion. Leakage from the lower cover or bonnet weep
hole indicates diaphragm rupture. For diaphragm
replacement, see Section 3.6.1, 3.7.1, or 3.8.1. On
sealed bonnet valves, back off the v-notch vent plug
two or three turns. CAUTION: When the process
fluid is hazardous or corrosive, extra precautions
should be taken, the user should employ appro-
priate safety devices and should be prepared to
control a leak of the process fluid. Fluid weeping
from the plug indicates a diaphragm failure.
Replace diaphragm immediately.
3.2 Pressurized Bonnet
Air pressure from the lower cover or bonnet weep
hole may indicate o-ring failure. Follow applicable
replacement instructions in Section 3.6, 3.7 or 3.8.