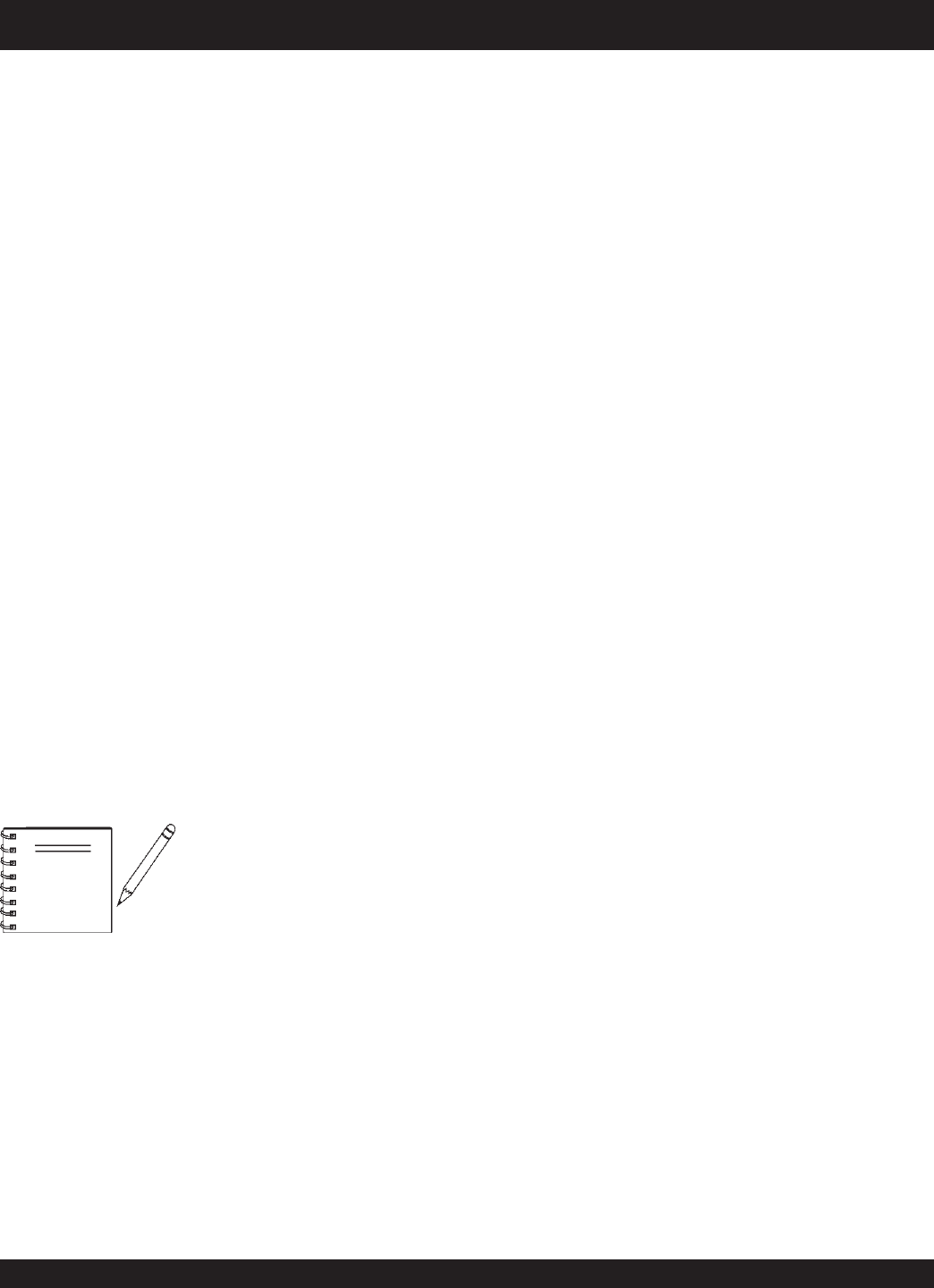
PAGE 40 — MAYCO C-30HDNI (PRECISION) PUMP — OPERATION AND PARTS MANUAL — REV. #7 (04/03/12)
C-30HDNI (PRECISION) PUMP — MAINTENANCE (PUMP)
Crankshaft and Cam Assembly Procedure
1. Set bearing block (P/N EM14303) into hydraulic press. Place
bearing cup into bearing block and press in evenly. Bearing
cup should be aligned equally on both sides of bearing block.
2. Set
crankshaft
into hydraulic press with the long end to-
wards the top. Install spacer (P/N EM14322), O-ring (P/N
EM14326) and bearing cone (P/N EM14325) onto crank-
shaft. Place bearing block on crankshaft until the bearing
cone is riding in the bearing cup.
3. Insert bearing cone spacer (P/N EM14323) onto crankshaft
and inside bearing block. Install second bearing cone until it
is seated inside bearing cup.
4. Place O-ring and spacer (P/N EM14302) on crankshaft. Set
cam weldment on top of spacer. Install crankshaft key and cam
key on cam bushing (P/N EM14301).
5. Slide cam bushing down crankshaft and align the bushing,
cam and crankshaft. Install sleeve over crankshaft and align
with hydraulic press. Install cam bushing bolts loosely. Press
bushing down onto bearing assembly. Leaving pressure on
the bushing, tighten cam bolts evenly to 40-50 foot pounds.
6. Release pressure on the bushing, reapply pressure to bush-
ing and tighten bolts evenly to 40-50 foot pounds. Repeat
procedure 3 to 4 times.
7. After bushing has been fitted tightly into cam, remove from
hydraulic press. Remove one bolt at a time, using Loctite,
install bolts and torque to 65-70 foot pounds. Counter sink set
screw hole and install dog point set screw and second set
screw both with Loctite
TM
.
8. Place cam bearing onto crankshaft keeping bearing loose.
Make sure the eccentric lock is
facing toward the outside of the
pumping unit.
9. Set crankshaft assembly into the pump box and align both
bearing assemblies with the pump box mountings.
10. After crankshaft assembly is securely fastened to the pump
box, place sprocket (P/N EM14307) onto the cam side of the
crankshaft assembly. Install bushing (P/N EM14309) into
sprocket. Align sprocket with sprocket on countershafts and
tighten bolts.
11. Install chain P/N EM14308. To adjust, loosen locknuts on
pusher bolts and tighten chain to approximately 1/2 in. slack
in the chain. Once chain is adjusted properly, tighten down
locknuts.
Ball and Seat Replacement Procedure
1. Remove 3”x 2” reducer and 3” elbow from the pump outlet.
Remove exhaust gate and Y-manifold (secondary manifold).
Check ball seat and ball stop pin for wear. If any wear is
detected, the part should be replaced. Remove T-manifold
(primary manifold). Check all parts for wear. Remove hopper
and hopper seat and inspect.
2. Loosen the piston nuts and remove the piston cup assembly
and cylinders. Inspect all parts for wear and replace parts with
excessive wear. Check oiler pump for proper operation.
3. Clean all parts thoroughly, removing all foreign material and
concrete slurry. Once parts are clean, install concrete cylin-
ders. Place oiler plate O-ring in place and coat with oil. Install
small O-ring on piston rod. Run oiler line through the cylinders
and connect in the oiler fitting on the oiler plate.
4. Push oiler plate into cylinder. Install ring and felt holder, soak
felt ring in oil, then install around felt holder in cylinder. Make
sure the bronze ring is flat, then push it up flush with the ring
and felt holder.
5. Coat piston cup with oil and push it into the cylinder. Install
bushing into center of piston cup. Put small O-ring on rod,
place face plate on rod and tighten down securely. Repeat
these procedure on the opposite cylinder.
6. Thoroughly check T-manifold, ball stoppings and both steel
balls for wear. Insert an O-ring in the top flange and in the
leading edge of the manifold. Put the manifold onto the
primary side of the pump and install bolts leaving them loose.
7. Check Y-manifold for wear, install all O-rings, ball stop pin, ball
and seat. Align and install Y-manifold to T-manifold and
cylinder assembly. Tighten Y-manifold bolts first before tight-
ening T-manifold bolts. After manifolds are tight, check O-rings
for slippage.
8. Insert seat into frame hole directly above the T-manifold. The
seat orifice should fit inside the frame itself, then the seat sits
on top of the orifice. On the dura-seat, set the big end of the
seat in the frame. The seat, or the small part of the dura-seat,
fits into the bottom of the hopper.
9. After tightening the manifold bolts and inserting the seats in
place, set the hopper over the seat and align the bolt holes.
Tighten bolts, check O-ring and seat for alignment.
10. Check exhaust gate for wear, install and align gate onto
Y-manifold. Insert O-ring into exhaust gate flange and close
gate. Lock down lever and adjust clamp arm.
11. Install 3 in. elbow and 3x 2 in. reducer. Fill hopper half full and
check for leaks.
NOTE