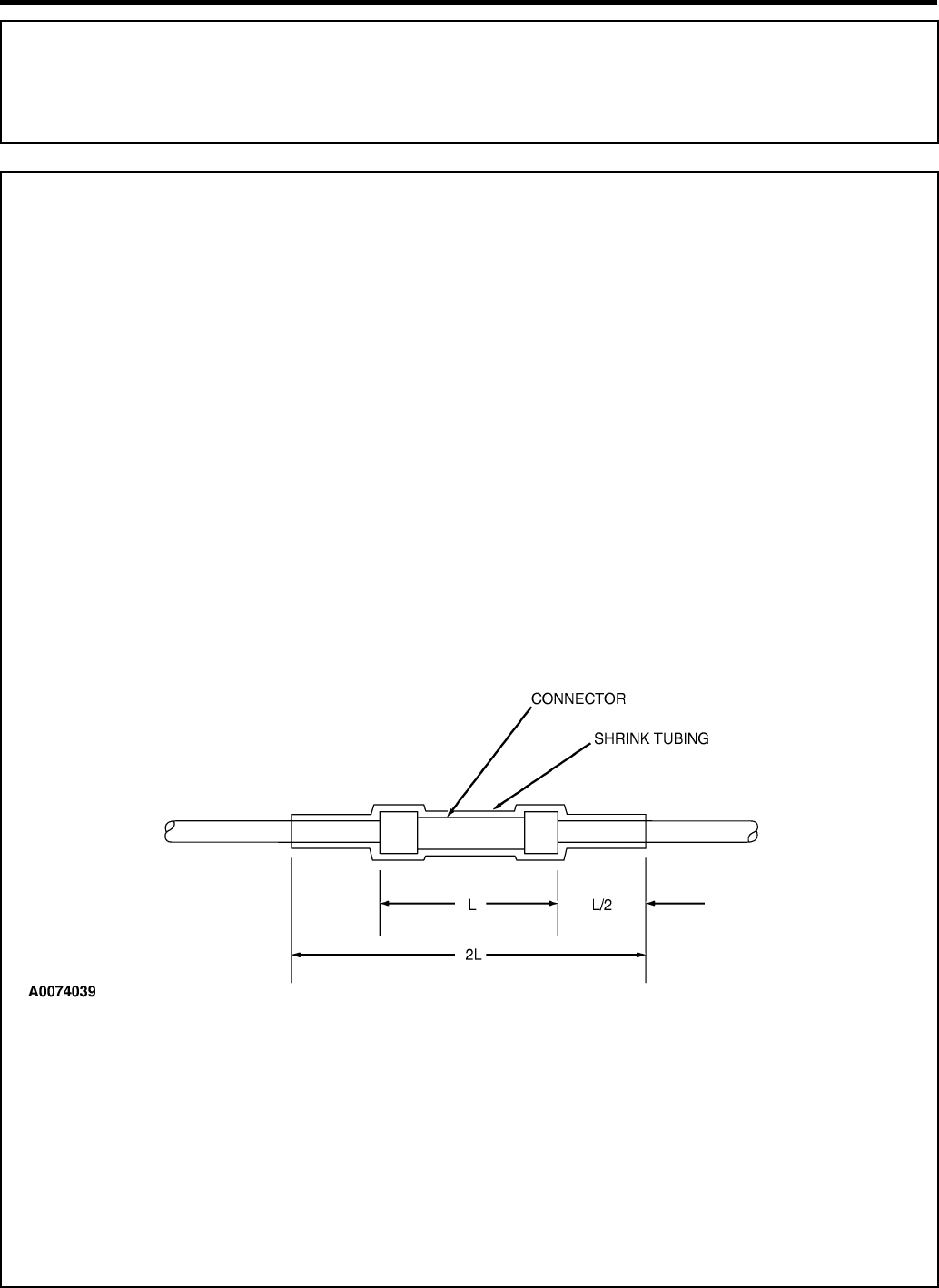
2-14 Electrical
Section 2: Electrical
Splices and Repairs
For quality splicing and to reduce potential problems, the following guidelines are recommended:
• Stagger the splices within a harness to reduce increased harness diameter. Splice only on
straight areas as installed, not on bends.
• Strip wire ends making sure that individual conductor strands are not damaged.
• When soldering, make sure an adequate mechanical joint exists before applying solder. Use only
resin-core solder. Acid-core solder should not be used since it may result in corrosion.
• For crimp joints, use butt-type metal barrel fasteners and the correct tool at the appropriate
setting for the wire size (such as Motorcraft® Crimp Tool S-9796) specifically designed for this
type of work.
• Make sure splice joints are adequately sealed and insulated. In an outside environment, use
Duraseal butt connectors or equivalent. A durable substitute splice joint can be achieved by
using a bare metal barrel, crimping, flow-soldering and covering with shrink tubing. Quality
electrical tape can be used inside the vehicle, but is not recommended for an outside
environment.
• Be sure that the new wire is not a lesser gauge than its original mating wire.
Recommended Splicing Method — Solder (For 16 AWG and Smaller Diameter Wire
Only)
1. Disconnect the battery ground cable.
2010 Expedition SSV Modifiers Guide, 07/2009