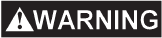
DO NOT TOW AT SPEEDS IN
EXCESS OF 20 MPH.
PACK WHEEL BEARINGS
1.
Chock all four wheels or hitch to tractor with en
-
gine off, key removed and parking brake set.
Jack empty trailer off ground and support with ad
-
equate jack stands.
2.
Disassemble hub and remove all old grease.
Clean bearings in non flammable solvent and
dry.
3.
Reassemble hub and pack with quality wheel
bearing grease.
4.
Adjust wheel bearing preload as described in the
following instructions
ADJUST WHEEL BEARING
PRELOAD
1.
Chock all four wheels or hitch to tractor with en-
gine off, key removed and parking brake set.
Jack empty trailer off ground and support with ad-
equate jack stands.
2.
Push back and forth on each wheel assembly. If
play is detected, bearings need adjusting.
3.
If adjusting bearings, it is suggested the bearings
be repacked as described previously.
4.
Remove hub cap and remove cotter pin from
spindle nut.
5.
Tighten spindle nut to remove all play. It should
be snug and slight drag can be felt while rotating
the wheel
6.
If the cotter pin hole in the spindle does not line
up with the notch in spindle nut, back off the spin
-
dle nut only enough to line up. Reinstall cotter
pin. If cotter pin is damaged, replace it.
7.
Replace hub cap and lower wheel to the ground.
FARM IMPLEMENT TIRES
SERVICE & MAINTENANCE TIPS
Agricultural tires are designed to carry a specified load
at a specified inflation pressure when mounted on a
specified width rim. When these conditions are met,
the deflection of the tire carcass is in the optimum
range and maximum tire performance can be
expected. If this combination of design factors is
altered for any reason, tire performance will be
reduced.
CHECKING INFLATION
Inflation pressures should be checked at least every
week. Recommended inflation Pressures based on
total load on tires should be used. For accurate
inflation use a special low-pressure gauge with
one-pound gradations. Gauges should be checked
occasionally for accuracy. Always use sealing valve
caps to prevent loss of air.
TIRE OVERLOAD OR UNDER INFLATION
Tire overload or under inflation have the same effect
of over-deflecting the tire. Under such conditions the
tread on the tire will wear rapidly and unevenly,
particularly in the shoulder area. Radial cracking in the
upper sidewall area will be a problem. With under
inflated drive tires in high torque applications sidewall
buckles will develop leading to carcass breaks in the
sidewall. While an under inflated drive tire may pull
better in some soil conditions, this is not generally true
and not worth the high risk of tire damage that such an
operation invites.
OVER INFLATION
Over inflation results in an under-deflected tire
carcass. The tread is more rounded, concentrates
tread wear at the centerline area. Traction is reduced
in high torque service because ground contact of the
tread shoulder area is reduced and the harder
carcass—with reduced flexing characteristics—does
not work as efficiently. The tightly stretched
over-inflated carcass is more subject to weather
checking and impact break damage.
PRESSURE ADJUSTMENTS REQUIRED-SLOW
SPEED OPERATION
Higher tire loads are approved for intermittent service
operations at reduced speed. Under such conditions
inflation pressure must be increased to reduce tire
deflection and assure full tire service life. See Page
13 for proper inflation.
USE OF PROPER WIDTH RIMS
Mention has been made of the importance of
mounting tires on rims of the specified width. When
this recommendation is not followed the following
conditions can result:
USE OF A RIM WIDER THAN RECOMMENDED
Use of a wider rim results in flattening of the tread
face. This feature may improve traction in some looser
soil conditions. In hard soils, however, the flatter tread
penetrates less effectively and tractive effort is
reduced. Additional stresses concentrated in the
shoulder area tend to increase the rate of shoulder
Tandem Trailer Page 11