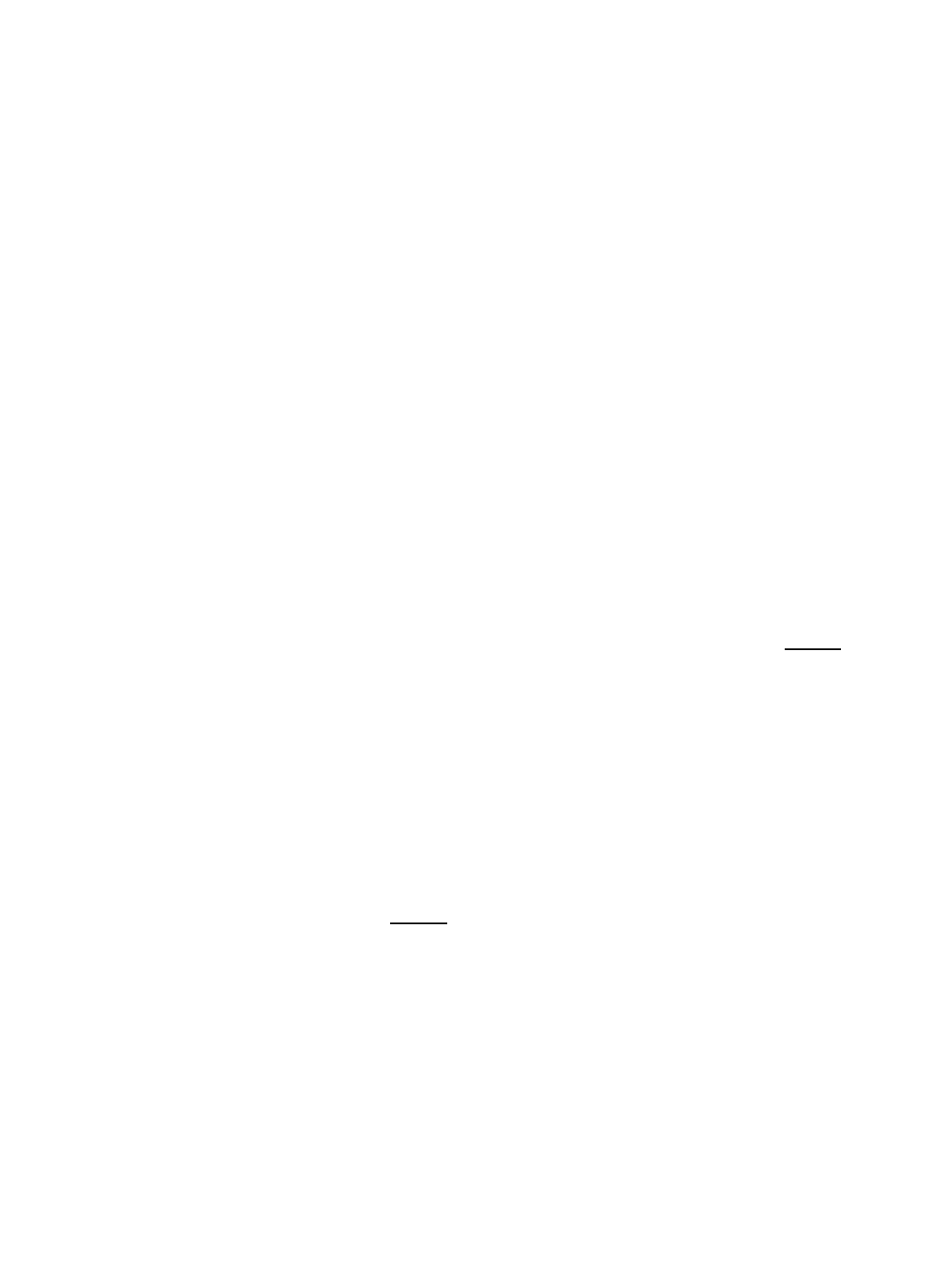
2001 Edelbrock Corporation
Brochure No. 63-0040
©
Rev. 11/01
Page 12 of 25
2.7 Fuel Solenoid Mounting and Installation
1. Hold the fuel solenoid securely (like in a bench vise) being careful not to harm the solenoid or block
the inlet or outlet of the solenoid.
2. Install 6AN X 1/4 NPT (Red straight fitting) fuel inlet fitting using liquid Teflon in the inlet port of the
fuel solenoid.
3. Install 4AN X 1/8 NPT (Red straight fitting) using liquid Teflon in the outlet port of the fuel solenoid.
4. Remove fuel solenoid assembly from vise.
5. Attach the universal solenoid mounting bracket to the bottom of the fuel solenoid using 2 of the
solenoid mounting screws.
6. Verify the desired mounting location of the fuel solenoid.
7. Install the fuel solenoid. If the solenoid mounting location is difficult to access, leave the solenoid
loose so the solenoid inlet and outlet port can be easily accessed.
8. Find a 1/4 NPT port or create your own on the fuel rail and install the supplied fitting into the port.
Connect the red steel braided line from the 1/4 NPT fitting to the inlet fitting on the fuel solenoid.
If using the 150hp jetting, it is recommended to get your fuel solenoid fuel supply from the fuel line
before it enters the rail. Just remember to check to be sure the fuel solenoid is recieving the proper
fuel pressure.
9. Leave the wires loose for the electrical system installation.
2.8 Nitrous/Fuel Solenoid Disassembly and Inspection
1. Close the valve on the nitrous bottle.
2. Empty the main nitrous supply line.
3. Remove the solenoid from the engine and securely clamp it to a vise, taking great care not to
damage the solenoid.
4. Remove the solenoid cover retaining nut from the top of the solenoid.
5. Remove the coil and housing from the solenoid base.
6. Unscrew the stem from the solenoid base. Do this by using a solenoid stem removal tool or by
“double nutting” the stem and unscrewing the stem from the housing body. Do not use pliers on
the solenoid stem; damage to the stem will result.
7. Remove the stem, spring and plunger from the solenoid base paying close attention to the way
they are assembled.
8. Examine the plunger seal for swelling, cuts and abrasions. The seal surface should be flat, except
for a small circular indentation in the center of the seal.
Note: A seal that has been contaminated or over-pressurized will bulge from exposure to
chemicals other than fuel or nitrous oxide. It can appear to extend down from the plunger and be
dome shaped. A contaminated seal may return to its original shape if left out in fresh air for
approximately 48 hours. It may then be returned to service. If it does not return to its original
shape, it must be replaced.
9. Clean the solenoid body. Do not use an oil-based solvent to clean any part of the solenoid.
Remove all foreign matter and dirt. Make sure solenoid body is clean, dry and free of oils before
assembly.
10. Replace the O-Ring, plunger and piston spring.
11. Re-assemble the solenoid by reversing the disassembly procedure.