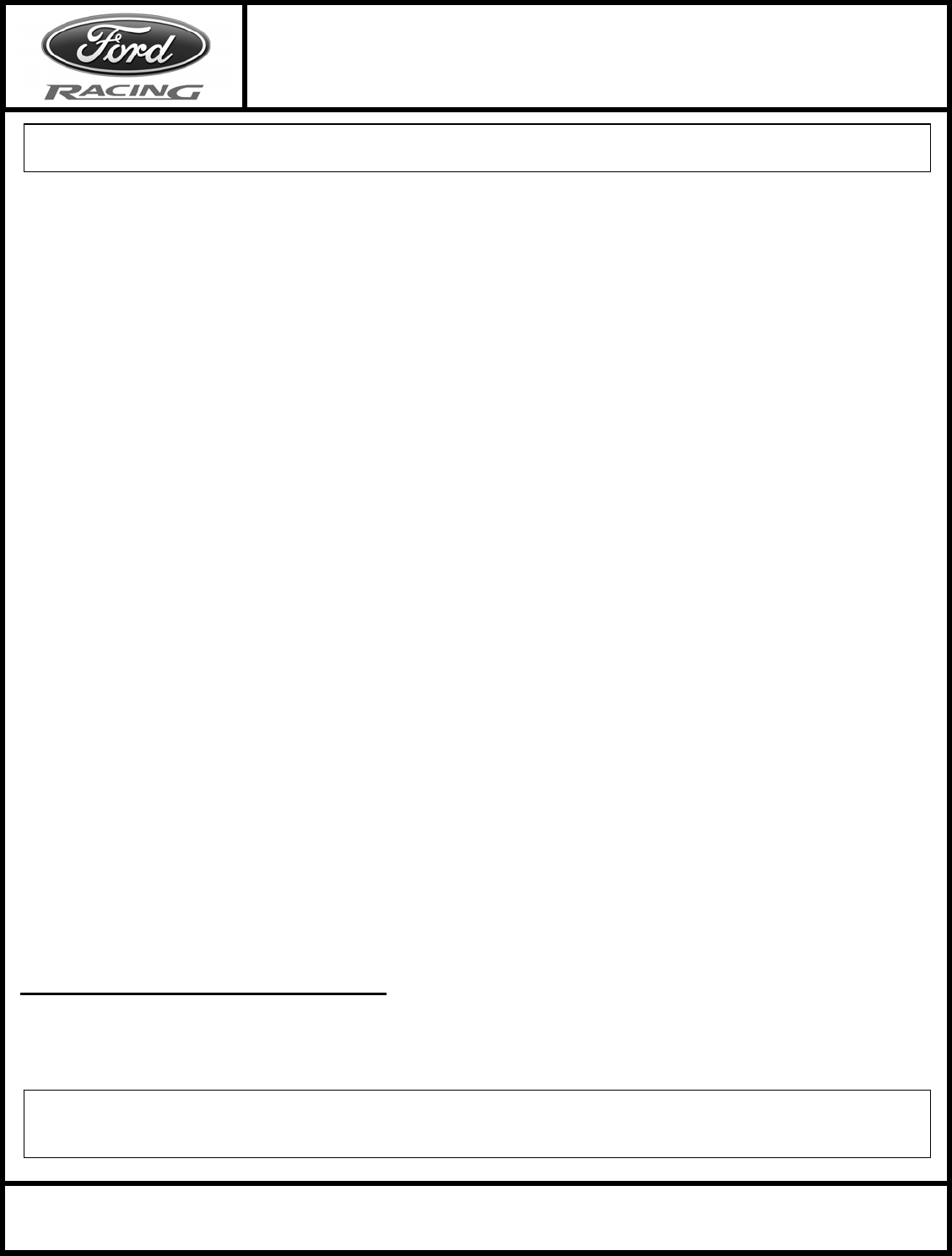
M-6007-X302E
340 HP Crate Engine
GUIDE
NO PART OF THIS DOCUMENT MAY BE REPRODUCED WITHOUT PRIOR AGREEMENT AND WRITTEN PERMISSION OF
FORD RACING PERFORMANCE PARTS.
IS-1850-0182
Page 9 of 13
Techline 1-800-367-3788
Factory Ford shop manuals are available from Helm Publications, 1-800-782-4356
STEP 9: Set timing. Tighten hold-down bolt.
COOLING SYSTEM
STEP 1: Fill cooling system (distilled/deionized water recommended).
STEP 2: The fill point of the cooling system must be the highest level of the cooling system.
STEP 3: Check for leaks.
STEP 4: After running engine and the cooling system is leak free, drain water and add appropriate amount
of water/coolant.
TRANSMISSION
Most small block engines come equipped with 157-tooth manual transmission flywheels. The billet steel flywheels
have multiple bolt patterns for different style pressure plates.
Sealer must be used on the small block flywheel to crankshaft bolts. Torque to 75-85 ft-lb. Over torquing will distort
rear main seal area and cause leakage.
A starter index plate is required between the block and transmission bell housing (all applications).
Be sure to install pressure plate alignment dowels if your pressure plate requires them.
For other transmission applications requiring different flywheels, see catalog or call the Techline for
other applications.
Verify that a pilot bearing is installed for all manual transmission applications. If using an automatic transmission,
be sure the pilot bearing is removed.
Verify proper bellhousing alignment on manual transmission applications. See bellhousing alignment.
Check crankshaft endplay of your engine before installing the transmission. After installing the transmission, check
crankshaft endplay. The number before and after installation should be the same. If endplay number is not the
same, this indicates that the components are incorrect, or improperly installed or damaged.
HOW TO CHECK BELLHOUSING ALIGNMENT:
The first step is to check bellhousing face runout. You are checking for parallelism of the back of the bellhousing to
the back of the block. Install the dial indicator (as shown in Fig. 2). Rotate the crankshaft and mark down the
reading. Be sure to push the crankshaft against the thrust bearing for an accurate reading. Maximum runout is .010.